WETEX, as the leading brand manufacturer of warping and sizing machines, has specialized in warp preparation machine manufacturing for over 20 years.
Our target is to promote Chinese warping and sizing machine advanced technology all over the world.
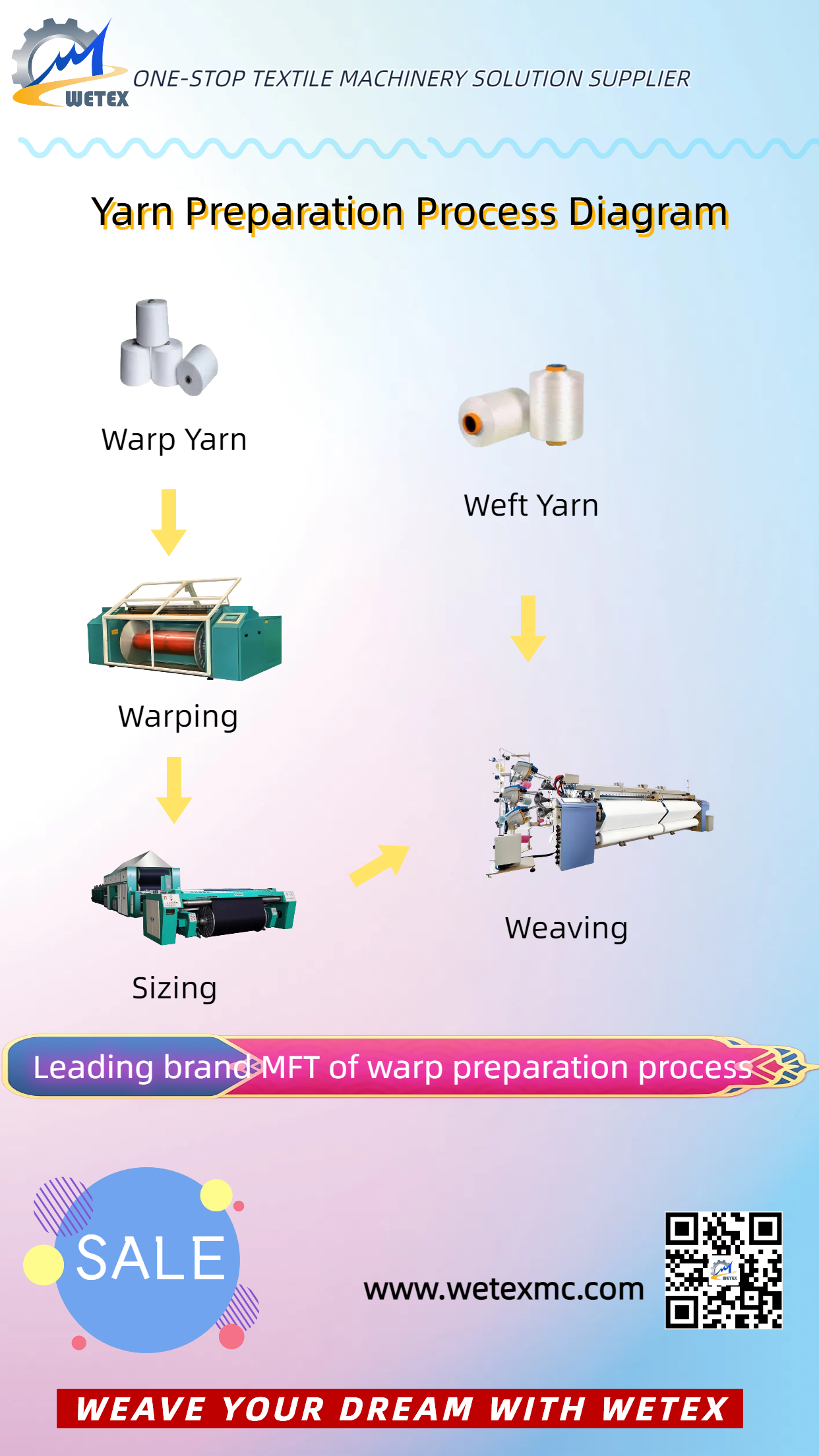
They are used in processes such as spinning, weaving, warping, and dyeing. Textile equipment can be used to manufacture, dye, and finish materials such as fiber, yarn, and thread.
Warping refers to the process of arranging yarns or threads lengthwise on a loom.
During warping, parallel threads are wound onto a beam in preparation for the weaving process.
This step ensures that the threads are properly aligned and tensioned before weaving.
The Importance of Warping:
Predetermined Yarn Length: It ensures the precise winding of a predetermined length of yarn, essential for maintaining consistency in production.
Combination of Packages: Warping allows the combination of multiple small packages into a unified beam, streamlining the weaving process
Types of warping process:
There are several types of warping processes, including direct warping, indirect warping, section warping, beam warping, and warping creel.
The choice of method will depend on the type and quantity of yarn, the final product desired, and the equipment available.
1. Direct Warping
This method is used for small-scale production and is a simple process of winding the yarn onto the warp beam.
The yarns are wound directly from the creel onto the warp beam without passing through a sizing bath.
2. Indirect Warping
This method is used for large-scale production. The yarns are wound onto a package, then the packages are arranged onto a beam.
The yarns are sized and dried, ensuring proper tension and preventing breakage during the weaving process.
3. Sectional Warping
This method is a combination of direct and indirect warping.
The yarns are wound onto packages, sized, and then arranged onto a beam in sections, allowing for easier management of the warp.
4. Ball Warping
Ball warping is a method of preparing the warp yarns for weaving in a circular formation.
The yarns are wound onto a large ball-shaped frame, forming a ball-warp.
The ball-warp is then taken to the loom, where it is threaded through the heddles and reed before being wound onto the warp beam.
The ball warping method is used to prepare a warp for smaller scale weaving, or when a large number of yarns are required,
as it allows for easier organization of the yarns and reduces the time and effort required to prepare the warp.
The operation of the warping process involves the following steps
1. Winding the yarn onto the warp beam:
The yarn is wound onto the warp beam in a parallel and uniform manner, with proper tension to avoid breakage.
2. Sizing the yarn:
The sized yarn is wound onto the warp beam to ensure proper tension and to protect the yarn from breakage during the weaving process.
3. Beam preparation:
The beam is prepared for use on the loom, including the installation of end-stops and the winding of the yarn onto the beam.
4. Threading the loom:
The warp threads are threaded through the heddles and reed to prepare for weaving.
Common problems that may arise during the warping process:
1. Skewing or distorting the fabric
This can occur due to uneven tension during the warping process, leading to an irregular warp beam.
2. Broken or weak yarns
This can be caused by over-beaming or improper winding of the yarn onto the warp beam.
3. Misaligned ends
This can result from uneven winding or insufficient tension during the warping process, leading to poorly spaced ends on the warp beam.
4. Length variations
This can be due to uneven winding or tension during the winding process, causing some yarns to be longer or shorter than others.
5. Cross threading
This occurs when the yarns become tangled or cross over one another during the winding process.
6. Inconsistent tension
This can cause irregular tension along the length of the warp, leading to warping defects in the final fabric.
By properly selecting the right type of warping process, following proper procedures, and using high-quality yarns, the quality, and consistency of the final woven fabric can be improved, and potential problems during the warping process can be minimized.
WETEX provides you with the most advanced and energy-efficient warping and weaving solutions. WETEX is a global brand grounded in more than two decades of experience of supplying indigenously designed warping and sizing machinery solutions of the world. please follow our website for more information www.wetexmc.com