The rapier weaving machine, a vital part of textile machinery, holds a significant position as one of the most prevalent weaving preparation machines within the textile industry. A crucial aspect in its operation is the consistency of warp tension during the warping process on the warping machine. When the warping tension is high on the warping machine, the warp yarns can be wound more densely, leading to a smaller thickness of each layer. In cases where the nominal fineness and the actual fineness of the yarn vary, it implies that the thickness of each layer of yarn also differs.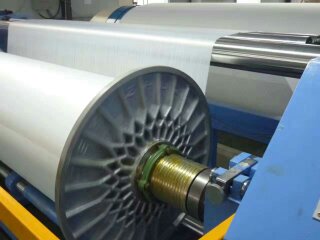
If the yarn is twisted, the degree of twisting has an impact on the thickness of the yarn. Additionally, the oil treatment content and dyeing color of the yarn frequently result in different friction coefficients, which in turn causes a disparity in tension. Consequently, in actual production, the calculation of the amount of traverse for the warping machine is not a straightforward task and is subject to significant fluctuations. This makes it challenging to define the production process precisely.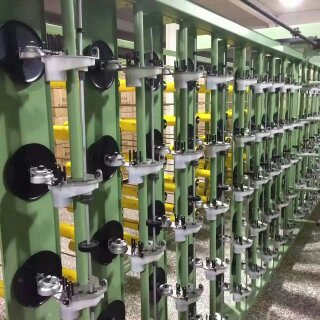
In the absence of a corresponding measuring device on the rapier weaving machine, the calculation of the transverse movement during warping on the sectional warper is often reliant on experience. However, even if the fineness appears to be exactly the same, differences in oil quantity can lead to varying friction coefficients, thereby affecting warping. Different tensions can also contribute to differences in warping density, ultimately leading to inaccurate calculations of the amount of lateral movement. Moreover, the fact that the nominal yarn fineness is identical does not guarantee that the actual fineness is the same; typically, there is a variance of around 1 - 2%, which means that the amount of traverse ought to be adjusted accordingly.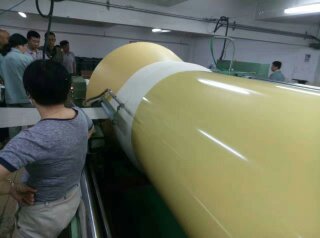
During the actual production process, the calculation of the traverse amount and the ability to correct any inaccuracies in a timely manner have long been issues that perplex manufacturers using sectional warpers. In the production of dipped and post-processed textiles, as well as the production of canvas for rubber conveyor belts, the core requirement is to ensure the consistency of the longitudinal tension of the canvas, with no allowance for tension differences. For more information on textile machinery like warping machines and weaving machines, visit wetexmc.com.