A sectional warping machine is a crucial component in the textile industry. It operates by dividing the total number of warp threads required for a fabric, based on the color matching cycle and the capacity of the creel, into several strips with an equal number of threads. Subsequently, these strips are wound parallel to the warping drum according to the specified width and length. Finally, all the warp threads are wound back onto the knitting shaft. It should be noted that sliver warping, which is similar in nature, involves dividing the total number of warp ends of a fabric into smaller parts, each of which is then wound in strips on a large roller. Once the required length is reached, the process involves shearing, consolidating, and then rolling article 2, article 3, and so on until all the processes are completed as per the design. After all the strips are rolled, they are unwound from the big drum and wound onto the weaving shaft. This process is integral to the efficient production of high-quality fabrics using a sectional warping machine.
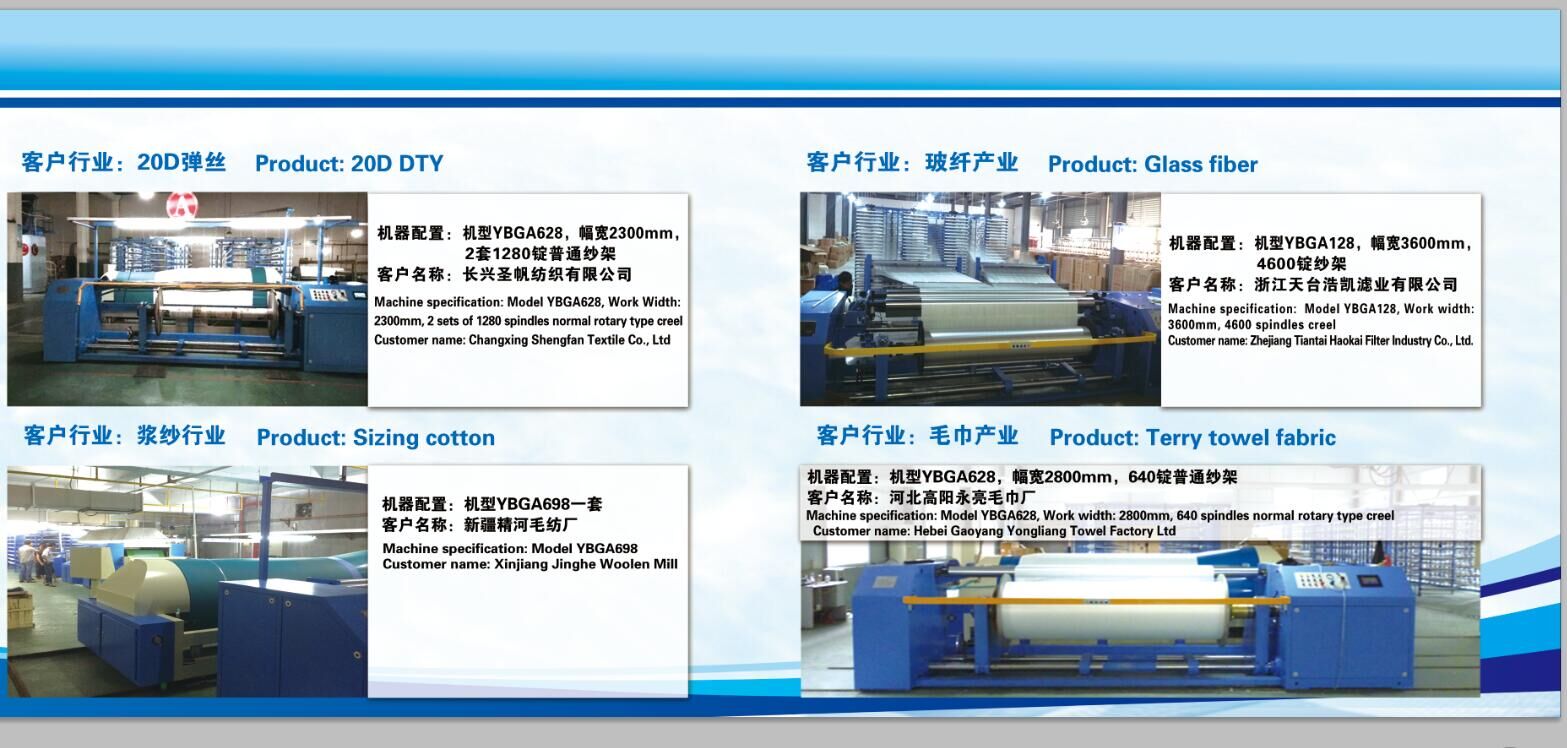
High Speed, Wide Width, and Strong Versatility: The sectional warping machine is characterized by its impressive technical specifications. With a roller speed of 600m/min and a width of 3.5m, it demonstrates high-speed operation and wide width coverage, making it suitable for all kinds of yarn and fiber types. This versatility allows textile manufacturers to produce a diverse range of fabrics with different materials and qualities, catering to various market demands.
Precise Control of Yarn Segment: The distance between the fixed-width reed and the winding point of the roller is maintained very short. As the winding diameter increases, this distance gradually recedes in a controlled manner to manage the free yarn segment effectively. This precise control mechanism ensures the stability and consistency of the yarn during the warping process, minimizing potential disruptions and errors.
Optimal Stability of Ribbon Ring: The fixed cone angle of the sectional warping machine is carefully designed to match the precise movement of the warping table. This combination achieves the best stability of the ribbon ring, which is crucial for maintaining the integrity and uniformity of the wound warp threads. The stable ribbon ring contributes to the overall quality of the fabric produced.
Enhanced Winding Quality: The weaving shaft of the sectional warping machine is equipped with a pressure device. This device ensures that the winding is well-formed, resulting in increased density of the wound yarn. Additionally, it helps to reduce the elastic loss of the yarn, thereby improving the mechanical properties and performance of the final fabric product.
The process flow of the sectional warping machine involves several key steps. It begins with warping, where the creel holds the bobbins of yarn. The yarn then passes through the back reed, split reed, and fixed reed in sequence, which helps to organize and align the warp threads. Finally, the yarn is inverted onto the axis, completing the warping process. This systematic process flow ensures the accurate and efficient preparation of the warp threads for subsequent weaving operations.
Winding Formation and Efficiency: The sectional warping machine employs a twice winding forming process, involving winding and rewinding one by one. While this method allows for precise control and organization of the warp threads, it does result in relatively low production efficiency compared to some other warping techniques. Additionally, there may be some unevenness in tension between each strip, which requires careful monitoring and adjustment to ensure the quality of the final product.
Pattern Arrangement and Process Simplification: One of the significant advantages of the sectional warping machine is its convenience in pattern arrangement. It enables the direct obtainment of the main shaft for products without the need for sizing, thereby shortening the overall process flow. This feature is particularly beneficial for small batch production of silk, wool, and yarn-dyed products, as it allows for greater flexibility and faster turnaround times in meeting specific design requirements.
Suitability for Specific Products: The sectional warping machine is highly suitable for the small batch production of silk, wool, and yarn-dyed products. Its ability to handle these materials with precision and flexibility makes it an ideal choice for manufacturers looking to produce high-quality, customized fabrics in relatively small quantities. This specialization in product range further highlights the unique capabilities and value of the sectional warping machine in the textile manufacturing process.
The sectional warping machine offers several distinct advantages in textile production. Firstly, its wide adaptability allows it to handle a variety of yarn and fiber types, enabling manufacturers to produce a diverse range of fabric products. Secondly, the convenient pattern arrangement feature simplifies the production process, reducing production time and costs, especially for small batch orders. Moreover, the machine generates less waste during the warping process, contributing to greater material efficiency and cost savings. Finally, the ability to directly obtain products without sizing from the warp splitter not only saves additional processing steps but also enhances the overall quality and performance of the final fabric. These advantages make the sectional warping machine a preferred choice for many textile manufacturers, especially those focusing on high-quality, customized fabric production.
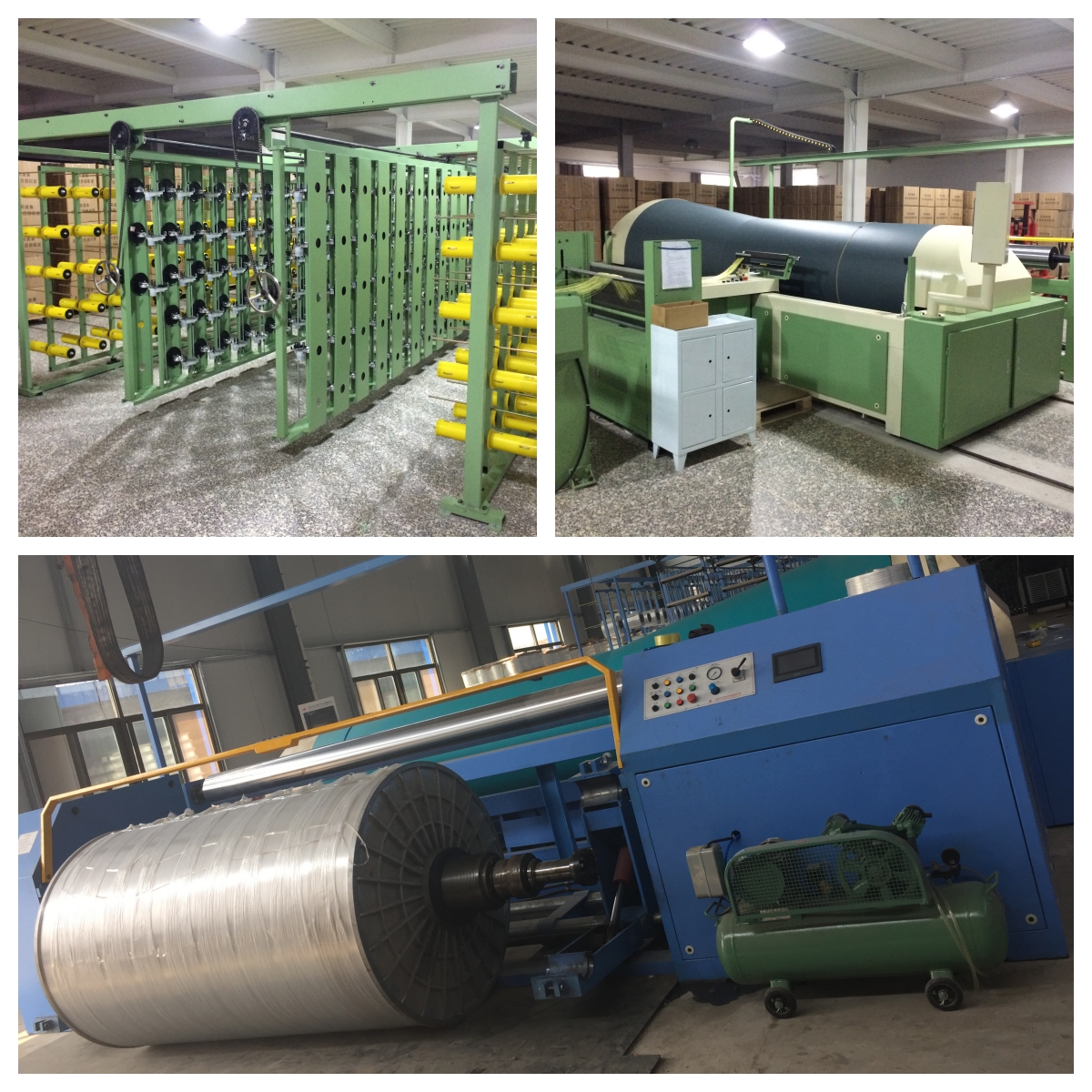
If you want to learn more about sectional warping machines or other textile machinery, you can visit wetexmc.com for detailed information and product offerings related to warping machines and other textile equipment.